Neodymium Iron Boron magnets are a type of rare earth alloy that typically has two atoms of Neodymium (Nd), 14 atoms of Iron (Fe), and one atom of Boron (B) as its primary elements, hence their chemical composition Nd2Fe14B, which is commonly abbreviated as NdFeB. There are other elements that are used to increase the coercivity, to gain lower oxidation characteristics, and to obtain other desirable characteristics. These elements are used to “dope” the alloy and are generally found in small quantities.
Sintered Neodymium Iron Boron Magnets
The sintered Neodymium Iron Boron magnet is produced by the OPS (orient-press-sinter) method. A crystalline alloy of Neodymium, Iron, and Boron is ground to a sub-micron powder using a ball mill, then aligned in a strong magnetic field, and pressed into a basic shape. The resultant “block” is then sintered, thereby fusing the material into a solid metal.
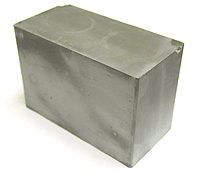
Generally, Neodymium Iron Boron magnets are sensitive to changes in temperature (reversible temperature coefficients being around -0.13%/°C). Additionally, they are more prone to oxidation than any other magnet alloy. Coating or plating is generally recommended unless using advanced alloys, such as MCE’s N3080, N3275, and N4467. MCE’s advanced grades are developed specifically for applications where the application of coating or plating is not desired. These advanced grades have oxidation rates that are far below the average Neodymium Iron Boron alloys, making them ideal for applications that require post assembly processing, due to tight tolerances in the final assembly state.
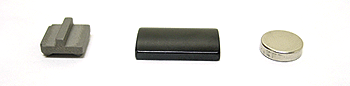
Neodymium Iron Boron magnets have some advantages over Samarium Cobalt magnets. Neodymium Iron Boron magnets are less expensive, since the main elements Nd and Fe are abundant, and are mechanically stronger. High energy products can be achieved. Small production runs have successfully yielded 58 MGOe nominal energy products; however, these are only achievable in the R&D state. Neodymium Iron Boron magnets are about 13% lighter than SmCo magnets. However, before deciding which material is better for you, review the comparisons between Neodymium Iron Boron and Samarium Cobalt.
Over the last 10 years, Neodymium Iron Boron magnets have become extremely popular in almost all high technology applications that require high performance magnets. Motors, sensors, computers, and microwave components are a few areas where Neodymium Iron Boron magnets are successfully used . The recent “miniaturization” of electronic and mechanical components is due to the high-energy products that are achieved using Neodymium Iron Boron magnets. Large capacity hard drives, feather weight head sets, and anti-lock braking systems have made tremendous leaps due to the Neodymium magnets.
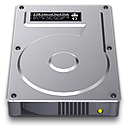
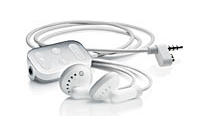
The selection of Neodymium Iron Boron magnets in your applications will depend on your working environment. If you use the magnets at elevated temperatures, select the alloys that have a high intrinsic coercivity (Hci). If you use the alloy at lower temperatures (such as room temperature), you may select higher Br materials. Remember that if the magnet is being used in adverse conditions, such as repelling positions in motors where repelling magnetic fields are being used to drive the rotor and similar applications, selecting materials with moderate or high coercivity is recommended. Applications where fields are being used to trigger sensors, switches, and similar applications may use lower coercivity magnets.
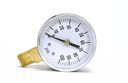
Using the Neodymium Iron Boron magnet in cryogenic temperatures (below 200°C) is not recommended.
Since the Neodymium Iron Boron magnets are prone to rapid oxidation, salt spray, salt water, and hydrogen are very harsh on the magnet. Consider hermetically sealing the magnet if you wish to use NdFeB in such environments. For high reliability applications, familiarize yourself with the section “testing and certification” so that you understand the tests that are available. Some of these tests are used to predict how the magnet will perform over extended periods in the field.
MCE offers the world’s premium Neodymium Iron Boron alloys, advanced coatings, and the ability to provide fast production runs. Additionally, MCE can manufacture and fabricate entire assemblies, such as rotor or stator assemblies, couplings, and hermetically sealed components to your requirements.
Bonded Neodymium Iron Boron Magnets
The bonded Neodymium Iron Boron materials are typically anisotropic. They can be made isotropic, and are manufactured using “binders,” such as epoxy resins or nylon to hold the powder in place, rather than “sintering” the alloy. Energy products of the bonded magnet range from 5 MGOe to 10 MGOe. Two basic processes are used:
- Compression Molding Binders are epoxy resins, and energy products of 10 MGOe are achievable. Moderately complex shapes can be achieved.
- Injection Molding Binders are generally nylon, but epoxy resins may also be used. Energy products are lower than compression molding; however, more complex shapes can be achieved without final processing, which makes it cost effective for low to medium performance applications which are cost sensitive.
The bonded Neodymium Iron Boron magnet may be used without surface treatment; however, coating is recommended. Generally, spray coatings are used, such has phenolic or epoxy coating.
A word of caution:
Do NOT use Neodymium Iron Boron magnets under the following conditions:
- In an acidic, alkaline, or organic solvent (unless you are going to hermetically seal the magnet inside a can)
- In water or oil (unless hermetically sealed, or you are prepared to accept a limited life)
- In an electrically conductive liquid, such as electrolyte containing water
- In a hydrogen-containing atmosphere, especially at elevated temperatures. Hydrogenation, a process where the Hydrogen molecule will react with the NdFeB, will occur, causing the magnet to rapidly deteriorate
- Environments containing corrosive gasses, such as Cl, NH3, Nox, etc.
- In the path of radioactive rays